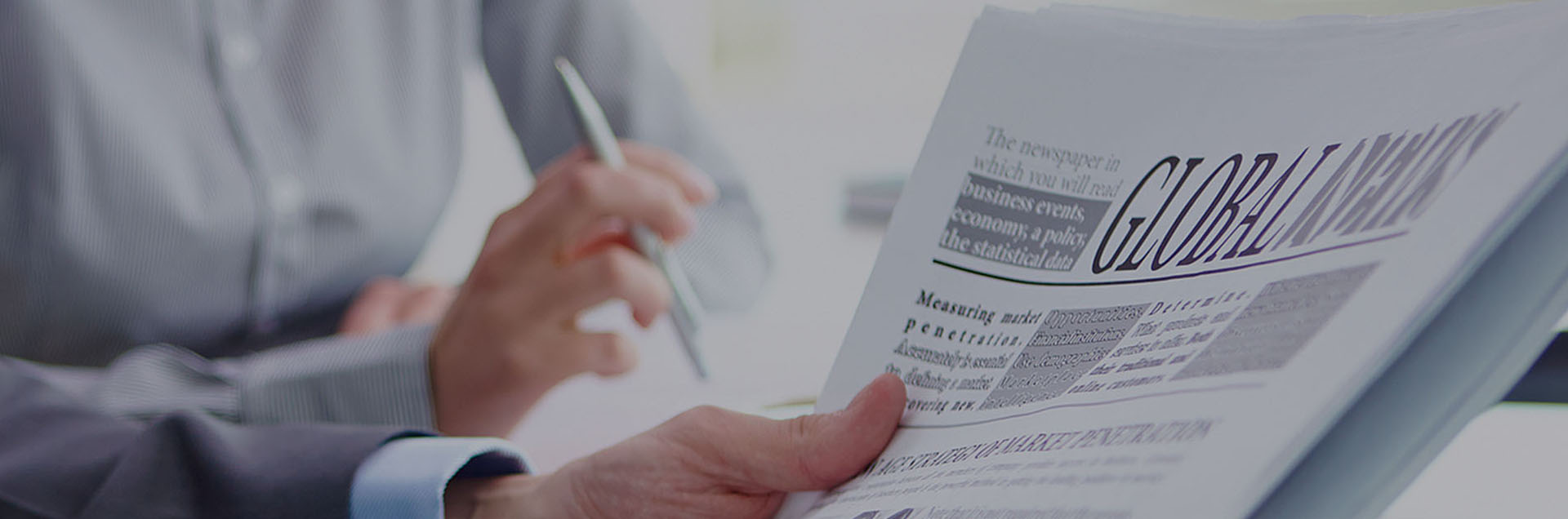
What is the principle of hydraulic system?
Release Time :
2025-01-24
Pascal's Law
Pascal's law or principle forms the theoretical foundation of hydraulic power systems and states that pressure applied to a confined fluid is transmitted uniformly and undiminished to all points within the fluid.
According to this principle, any force applied to a confined fluid (such as hydraulic oil in a cylinder) results in an increase in pressure that propagates throughout the system. The extent to which the force is distributed depends on the size, shape, and overall design of the system. By utilizing Pascal's law, hydraulic power systems enable engineers to transmit force over great distances and amplify it, providing precise power control for a variety of applications.
Best practices to ensure efficient pressure transmission:
Use high-quality hydraulic fluid with the correct viscosity.
Minimize the risk of leaks and air entrapment in hydraulic lines.
Maintain constant pressure throughout the system.
Continuous flow of fluid
For a hydraulic system to operate efficiently, a continuous flow of fluid must be maintained. The continuity equation states that the fluid flow rate remains constant throughout the system, meaning that the product of the cross-sectional area and the flow rate at any point is constant. In other words, if the area is narrowed, the fluid viscosity increases, and vice versa.
Optimal flow is achieved by creating a closed-loop configuration that connects core components such as pumps and valves. The pump is really the heart of the system, ensuring fluid flows as required to accomplish the intended work. Meanwhile, valves enable precise directional and flow control for targeted performance.
Best practices for optimizing fluid flow in hydraulic systems include:
Specifying correctly sized and rated hoses, pipes, and valves.
Avoid sharp bends and unnecessary changes in flow direction.
Monitor and control flow rates throughout the system to avoid cavitation.
Pressure and flow control
Pressure and flow control, or energy balance, are essential elements in hydraulic system design to maximize efficiency and safety. A system’s flow and pressure directly impact its ability to maintain the desired velocity or force level when a load is applied. Bernoulli’s principle states that as a fluid flows through a system, an energy exchange occurs between its kinetic, potential, and pressure energies.
Pressure and flow are regulated by pressure relief valves and flow control valves to prevent over-pressurization of the system and to regulate the velocity of the hydraulic fluid to ensure steady and controlled motion.
Best practices for maintaining energy balance in a hydraulic system:
Optimize pump and motor selection to meet the power requirements of your application.
Use correctly sized and configured accumulators to store energy.
Incorporate energy recovery technologies such as regenerative circuits.
Fluid Selection and Maintenance
Choosing the right fluid is critical to efficient power transmission and system performance. To achieve overall system efficiency, the selected fluid must have the proper viscosity, optimal temperature performance, and resistance to chemical degradation and wear. Regular maintenance and fluid replacement is essential to ensure reliable hydraulic operation - this may involve scheduled oil changes, fluid analysis, and filtration programs to minimize the risk of contamination.
Best practices include:
Choosing a fluid type that is compatible with your system materials and optimized for the specific application and operating conditions.
Implementing a fluid testing and monitoring program to keep contamination levels within acceptable limits for the application.
Heat Dissipation and Management
Closed hydraulic systems are designed to minimize heat dissipation and conserve energy, but despite this, strict temperature management is critical to maintaining the life and performance of any hydraulic system. Excessive temperatures can affect the efficiency of the system by degrading fluid quality, reducing sealing, and increasing the risk of leaks.
Best practices for thermal management in hydraulic systems include the use of heat exchangers, cooling fans, and radiators - engineers must design systems that can maintain optimal temperature levels and ensure adequate heat dissipation to avoid overheating.
RELATED NEWS
2025-02-28
How to diagnose hydraulic problems?
The Importance of Hydraulic Systems in Industrial ApplicationsHydraulic systems are widely used in industries such as construction, manufacturing, agriculture, and aerospace due to their ability to generate significant force with precise co···
2025-02-28
What is the life expectancy of a hydraulic cylinder?
Typical Life Expectancy of a Hydraulic CylinderThe life expectancy of a hydraulic cylinder can vary widely depending on its design, application, and operating environment. On average, a well-maintained hydraulic cylinder can last anywhere f···
2025-02-28
Why is my hydraulic cylinder not retracting?
The Role of Hydraulic Cylinders in Mechanical SystemsHydraulic cylinders are the backbone of many industrial applications, from construction equipment to manufacturing machinery. They operate by converting hydraulic energy into linear motio···
2025-02-28
How to check if a hydraulic cylinder is leaking internally?
Hydraulic cylinders are essential components in many industrial and mechanical systems, providing the force needed to perform heavy-duty tasks with precision. However, like any mechanical system, hydraulic cylinders are susceptible to wear ···
2025-02-28
What is the most common failure on a hydraulic cylinder?
The Role of Hydraulic Cylinders in Industrial ApplicationsHydraulic cylinders are the workhorses of many industrial systems, providing the force required to perform heavy-duty tasks. They consist of a cylindrical barrel, piston, piston rod,···
2025-02-21
What is the most commonly used hydraulic cylinder?
The Most Commonly Used Hydraulic CylinderThe tie-rod hydraulic cylinder is widely regarded as the most commonly used hydraulic cylinder. Its popularity stems from its simple design, ease of maintenance, and cost-effectiveness. Tie-rod cylin···

GET YOUR FREE QUOTE
We will contact you within 24 hours. ( WhatsApp/facebook:13665121168)