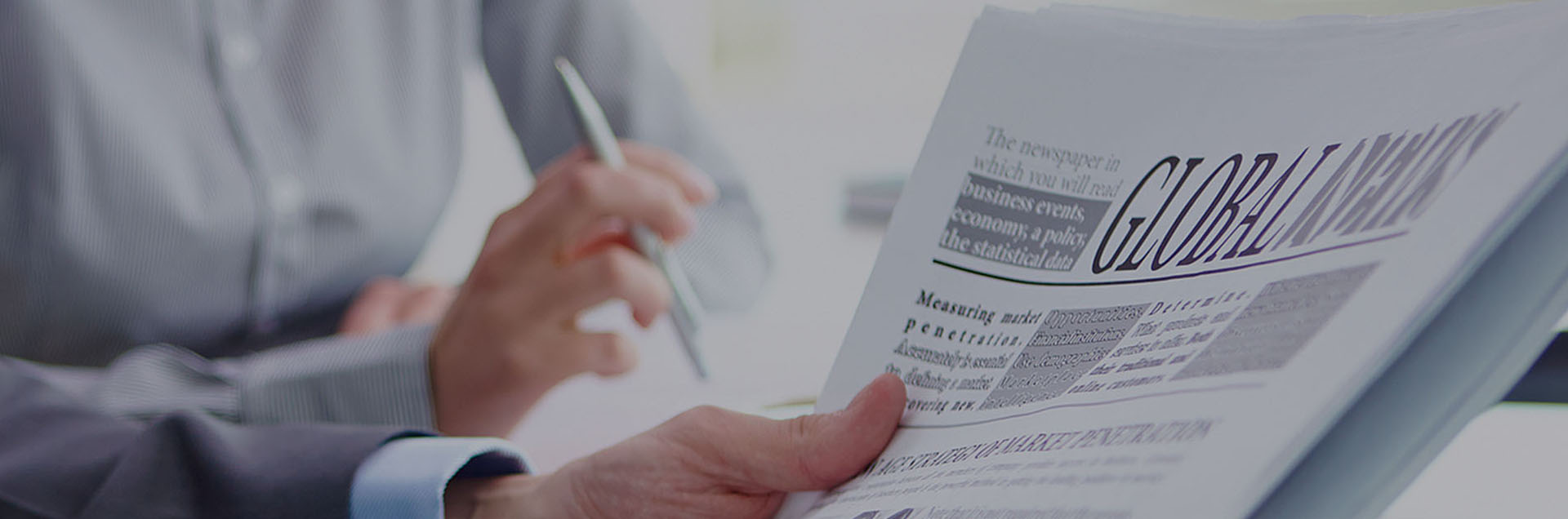
How to diagnose hydraulic problems?
Release Time :
2025-02-28
The Importance of Hydraulic Systems in Industrial Applications
Hydraulic systems are widely used in industries such as construction, manufacturing, agriculture, and aerospace due to their ability to generate significant force with precise control. These systems rely on hydraulic fluid, pumps, valves, cylinders, and other components to transmit power and perform work. When a hydraulic system malfunctions, it can lead to reduced performance, increased energy consumption, and even equipment failure. Understanding how to diagnose hydraulic problems is crucial for minimizing downtime and ensuring the system operates at peak efficiency.
Common Signs of Hydraulic Problems
Before diving into diagnostic methods, it’s important to recognize the symptoms of hydraulic system issues. Common signs include:
1.Reduced Performance:
The system may struggle to generate the required force or operate slower than usual.
2.Unusual Noises:
Knocking, whining, or grinding sounds can indicate issues such as cavitation, air in the system, or worn components.
3.Overheating:
Excessive heat in the hydraulic fluid or components can signal problems like fluid contamination, blocked lines, or overloading.
4.Leaks:
Visible hydraulic fluid leaks around seals, hoses, or connections are a clear sign of a problem.
5.Erratic Operation:
Inconsistent or jerky movements in hydraulic cylinders or actuators may point to issues with valves, pumps, or fluid flow.
6.Increased Energy Consumption:
A sudden spike in energy usage can indicate inefficiencies within the hydraulic system.
Step-by-Step Guide to Diagnosing Hydraulic Problems
Diagnosing hydraulic problems requires a systematic approach to identify the root cause and implement effective solutions. Here are the key steps to follow:
1. Visual Inspection
Check for visible signs of damage, leaks, or wear on hoses, seals, and connections.
Inspect the hydraulic fluid reservoir for proper fluid levels and contamination.
2. Check Hydraulic Fluid
Examine the fluid for discoloration, cloudiness, or debris, which can indicate contamination.
Test the fluid’s viscosity and temperature to ensure it meets the system’s requirements.
3. Monitor System Pressure
Use a pressure gauge to measure the system’s pressure at various points.
Compare the readings to the manufacturer’s specifications to identify abnormalities.
4. Inspect Filters and Strainers
Clogged or dirty filters can restrict fluid flow and cause system inefficiencies.
Replace or clean filters as needed.
5. Test Components Individually
Isolate and test components such as pumps, valves, and cylinders to identify faulty parts.
Listen for unusual noises or observe irregular movements during testing.
6. Check for Air in the System
Air bubbles in the hydraulic fluid can cause spongy operation and reduce efficiency.
Bleed the system to remove trapped air.
7. Review System Design and Operation
Ensure the system is operating within its design parameters, including load limits, pressure settings, and temperature ranges.
Verify that all components are properly sized and compatible.
Common Hydraulic Problems and Their Causes
Understanding the root causes of hydraulic problems can help streamline the diagnostic process. Here are some common issues and their potential causes:
1.Cavitation:
Caused by low fluid levels, restricted intake lines, or excessive pump speed.
Leads to damage to pump components and reduced system performance.
2.Overheating:
Often caused by excessive load, fluid contamination, or inadequate cooling.
Can result in seal failure and accelerated wear on components.
3.Leaks:
Typically caused by worn seals, damaged hoses, or loose connections.
Leads to fluid loss, reduced efficiency, and environmental hazards.
4.Slow or Erratic Operation:
May be due to air in the system, worn valves, or insufficient fluid flow.
Results in inconsistent performance and reduced productivity.
5.Excessive Noise:
Often caused by cavitation, air entrapment, or worn bearings.
Indicates potential damage to pumps or other components.
Best Practices for Preventing Hydraulic Problems
Preventing hydraulic problems is more cost-effective than repairing them. Here are some best practices to keep your hydraulic system running smoothly:
1.Regular Maintenance:
Schedule routine inspections and servicing to identify and address issues early.
2.Use High-Quality Fluid:
Ensure the hydraulic fluid meets the system’s specifications and is free of contaminants.
3.Monitor Operating Conditions:
Avoid overloading the system and operate within recommended temperature and pressure ranges.
4.Train Operators:
Educate operators on proper usage and early signs of potential issues.
5.Keep the System Clean:
Use proper filtration and sealing to prevent contamination.
Conclusion
Diagnosing hydraulic problems is a critical skill for maintaining the efficiency and reliability of hydraulic systems. By recognizing common signs of issues, following a systematic diagnostic approach, and implementing preventive measures, operators can minimize downtime and extend the lifespan of their hydraulic systems. As hydraulic technology continues to evolve, understanding how to diagnose and resolve problems will remain essential for achieving optimal performance and operational success. With proper care and attention, hydraulic systems can deliver consistent, reliable power, driving productivity and innovation across industries.
RELATED NEWS
2025-02-28
How to diagnose hydraulic problems?
The Importance of Hydraulic Systems in Industrial ApplicationsHydraulic systems are widely used in industries such as construction, manufacturing, agriculture, and aerospace due to their ability to generate significant force with precise co···
2025-02-28
What is the life expectancy of a hydraulic cylinder?
Typical Life Expectancy of a Hydraulic CylinderThe life expectancy of a hydraulic cylinder can vary widely depending on its design, application, and operating environment. On average, a well-maintained hydraulic cylinder can last anywhere f···
2025-02-28
Why is my hydraulic cylinder not retracting?
The Role of Hydraulic Cylinders in Mechanical SystemsHydraulic cylinders are the backbone of many industrial applications, from construction equipment to manufacturing machinery. They operate by converting hydraulic energy into linear motio···
2025-02-28
How to check if a hydraulic cylinder is leaking internally?
Hydraulic cylinders are essential components in many industrial and mechanical systems, providing the force needed to perform heavy-duty tasks with precision. However, like any mechanical system, hydraulic cylinders are susceptible to wear ···
2025-02-28
What is the most common failure on a hydraulic cylinder?
The Role of Hydraulic Cylinders in Industrial ApplicationsHydraulic cylinders are the workhorses of many industrial systems, providing the force required to perform heavy-duty tasks. They consist of a cylindrical barrel, piston, piston rod,···
2025-02-21
What is the most commonly used hydraulic cylinder?
The Most Commonly Used Hydraulic CylinderThe tie-rod hydraulic cylinder is widely regarded as the most commonly used hydraulic cylinder. Its popularity stems from its simple design, ease of maintenance, and cost-effectiveness. Tie-rod cylin···

GET YOUR FREE QUOTE
We will contact you within 24 hours. ( WhatsApp/facebook:13665121168)