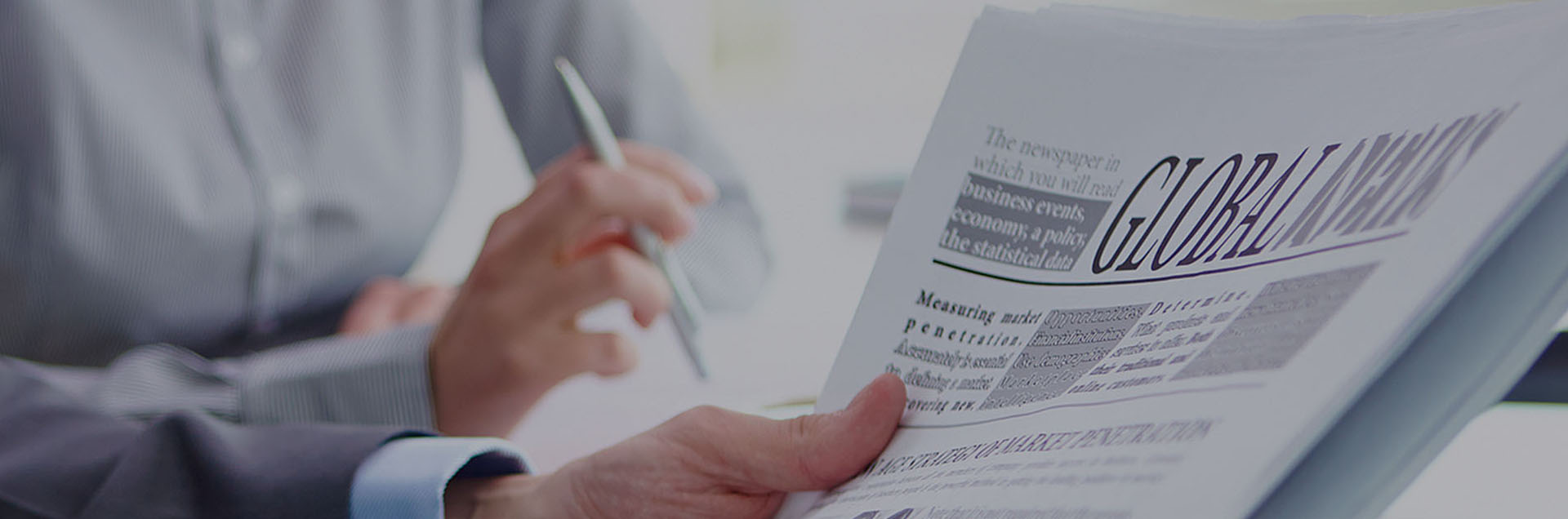
What are the 2 basic types of hydraulic systems?
Release Time :
2025-01-23
Closed-Loop Hydraulic Circuits
A closed-loop hydraulic system, sometimes called a "hydrostatic drive," is a type of hydraulic system that can be used in mobile equipment such as skid steers and bulldozers, and industrial machinery such as conveyors.
Fluid flows directly from the piston pump to the motor and back without passing through a reservoir in a hydrostatic drive. The speed and direction of the fluid controls the motor, and because it is a simple closed loop, the system can operate in both directions.
This system has a displacement controller (control lever) mounted on the swashplate of the piston pump to adjust the speed and direction. The pump's swashplate angle is set to supply fluid to the motor when the control lever is moved forward and the motor starts to turn. When the user presses the control lever forward, the swashplate angle increases, causing more fluid displacement. Therefore, more fluid is supplied to the motor, causing it to turn faster.
When the operator pulls the control lever back to the neutral position, the fluid flow automatically stops. However, when the same control lever is pulled back in the opposite direction, the displacement direction is reversed. This again sends fluid in the opposite direction, causing the motor to turn in the opposite direction. Therefore, closed-loop hydraulic systems often provide an effective way to control the direction and speed of a motor.
Open-loop hydraulic circuits
Open-loop hydraulic circuits are mainly used to drive linear actuators such as hydraulic cylinders. They are used on mobile machinery such as excavators and cranes, as well as industrial machinery such as hydraulic presses.
Open-loop hydraulic systems connect a reservoir to the pump inlet and the actuator return port. Unlike closed-loop circuits, the pump provides a continuous flow of fluid to the system. After the fluid flows through the system and returns to the reservoir, fresh fluid is drawn from the reservoir and pumped back into the system.
The direction and speed of the actuator are mainly achieved by the flow regulating valve and directional control valve located between the pump and the actuator. When the spool position in the directional control valve is switched, the direction of fluid flow to and out of the actuator changes. When the aperture of the variable orifice in the flow regulating valve opens or closes, it increases or decreases the flow of fluid to the actuator. This causes the hydraulic engineering system to accelerate or decelerate accordingly.
When the directional control valve directs flow to the actuator, the load acting on the actuator causes the pressure in the circuit to increase, allowing work. When the system pressure reaches a specified level, the pressure relief valve opens and directs the oil to the tank, thereby regulating the pressure in the circuit. When no work is required, the oil flow is diverted from the actuator to the tank, so that there is no flow resistance and therefore no pressure in the circuit.
RELATED NEWS
2025-02-28
How to diagnose hydraulic problems?
The Importance of Hydraulic Systems in Industrial ApplicationsHydraulic systems are widely used in industries such as construction, manufacturing, agriculture, and aerospace due to their ability to generate significant force with precise co···
2025-02-28
What is the life expectancy of a hydraulic cylinder?
Typical Life Expectancy of a Hydraulic CylinderThe life expectancy of a hydraulic cylinder can vary widely depending on its design, application, and operating environment. On average, a well-maintained hydraulic cylinder can last anywhere f···
2025-02-28
Why is my hydraulic cylinder not retracting?
The Role of Hydraulic Cylinders in Mechanical SystemsHydraulic cylinders are the backbone of many industrial applications, from construction equipment to manufacturing machinery. They operate by converting hydraulic energy into linear motio···
2025-02-28
How to check if a hydraulic cylinder is leaking internally?
Hydraulic cylinders are essential components in many industrial and mechanical systems, providing the force needed to perform heavy-duty tasks with precision. However, like any mechanical system, hydraulic cylinders are susceptible to wear ···
2025-02-28
What is the most common failure on a hydraulic cylinder?
The Role of Hydraulic Cylinders in Industrial ApplicationsHydraulic cylinders are the workhorses of many industrial systems, providing the force required to perform heavy-duty tasks. They consist of a cylindrical barrel, piston, piston rod,···
2025-02-21
What is the most commonly used hydraulic cylinder?
The Most Commonly Used Hydraulic CylinderThe tie-rod hydraulic cylinder is widely regarded as the most commonly used hydraulic cylinder. Its popularity stems from its simple design, ease of maintenance, and cost-effectiveness. Tie-rod cylin···

GET YOUR FREE QUOTE
We will contact you within 24 hours. ( WhatsApp/facebook:13665121168)